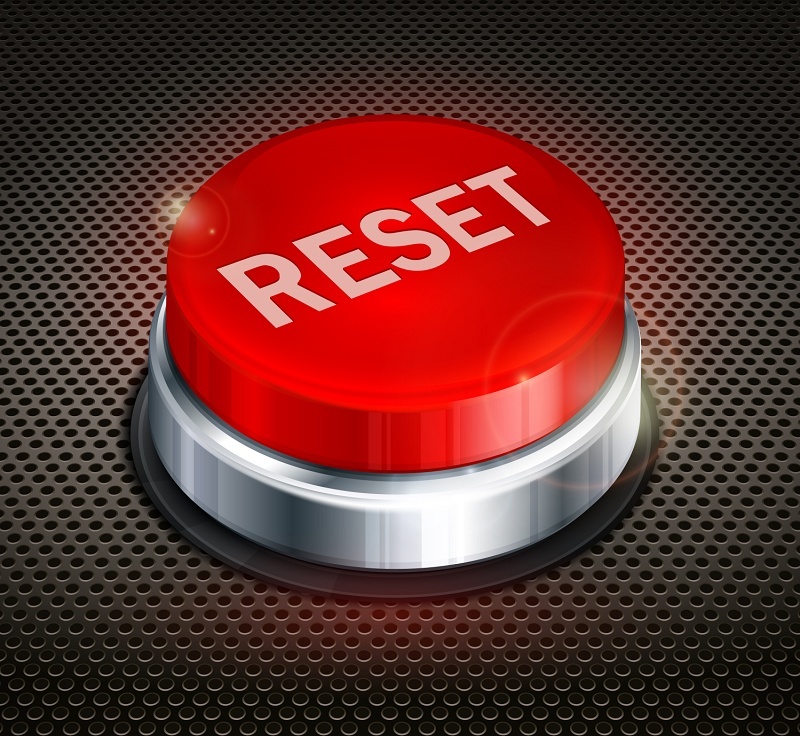
Pushing the Supply Chain Reset Button
Over the last three years, these three fundamental assumptions unraveled: they are no longer valid. The impact varies by supply chain sector and value chain.
Over the last three years, these three fundamental assumptions unraveled: they are no longer valid. The impact varies by supply chain sector and value chain.
As my arms stretch forward to pull for the next lap in the summer heat, three thoughts circulate in my head. (I often write my
What is the role of planning? The goal should be organizational alignment to potential issues and outcomes.
Supply chain excellence is easier to say than to explain. Business leaders are action-oriented and competitive. Executive teams strive to drive improvement in supply chain
As a child, I never painted within the lines. Always as a non-conformist, I pushed the edges and challenged boundaries. I discovered, as an adult,
I wrote my first report on Sales and Operations Planning (S&OP) while sitting on the floor in the Atlanta airport in 2005 when I was
Uncanny. The US GDP in 2021 grew at an unexpected rate of 5.7% in the second year of the pandemic. To understand the phenomenon, the 2019
My quest to build holistic thinking in organizations stretches over many decades. It is easy to say “be a holistic thinker”, but it is harder
As I rolled holiday cookies in my hands, I watched TV. I seethed as the news stations celebrated supply chain success for the December holidays.
It is that time of year. Yes, a time when well-meaning supply chain leaders share their strategy decks for the upcoming year and ask me