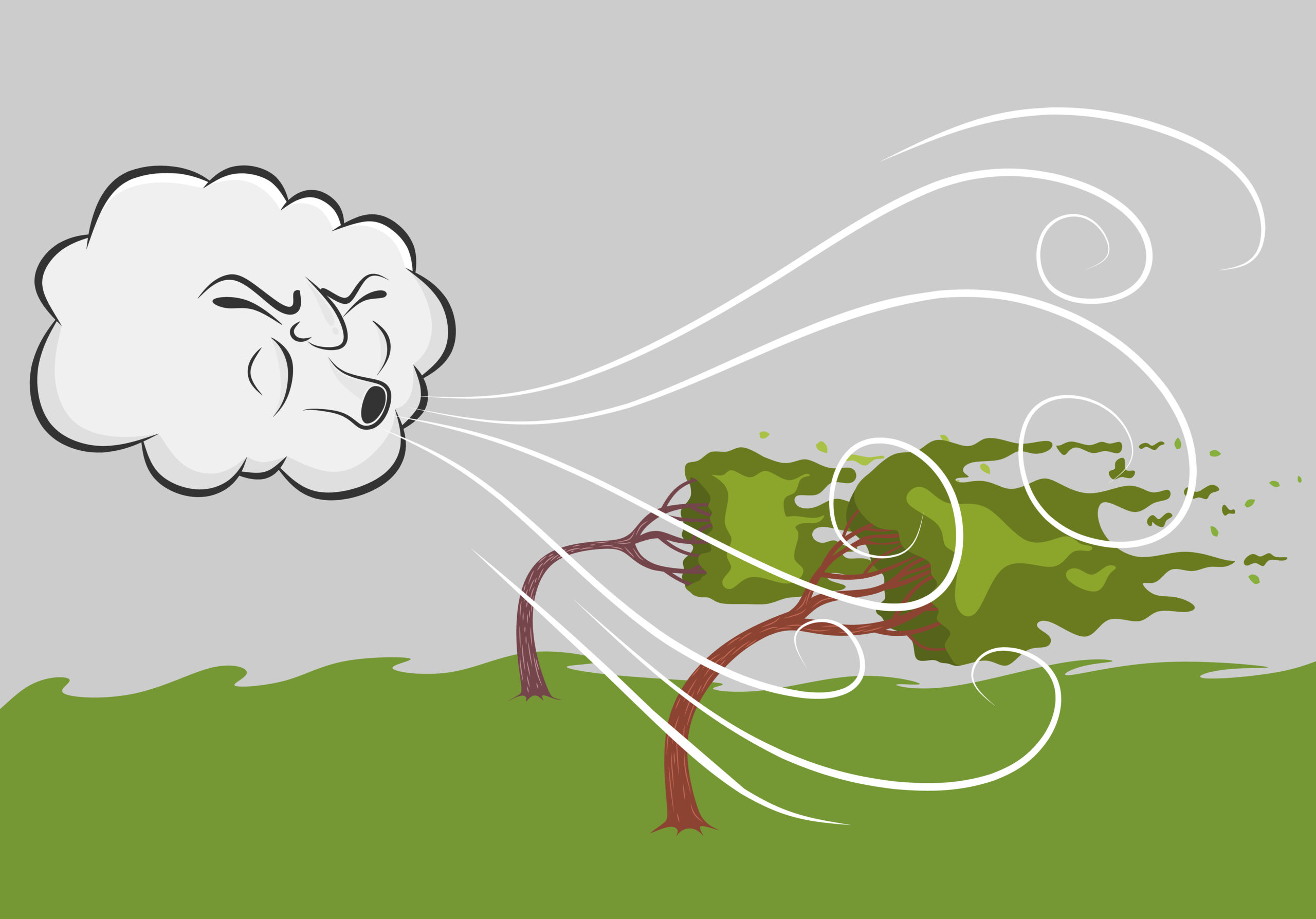
As The Winds Blow: Improving Supply Chain Planning
The winds of change transform industries. Does a digital transformation add value? Who knows? The answer is blowing in the wind because there is no
The winds of change transform industries. Does a digital transformation add value? Who knows? The answer is blowing in the wind because there is no
The use of pattern recognition and orbit charts to study supply chain excellence.
Concerned about the impact of the Gartner Top 25 on the market, Lora Cecere, Founder of Supply Chain Insights, shares insights on the performance of the companies selected to be on the list.
In this blog, we challenge traditional thinking to embrace supply chain planning to better manage a complex system that is growing in complexity. Here, I share insights on the Leverage Points in the Supply Chain as places to start. The blog builds from the Donella Meadows Project.
In this post, I explore the definition of supply chain excellence and the challenge of resilience.
View Post I miss the work conversations by the coffee pot. Especially the old-fashioned ones that forced teams to linger and talk with colleagues as
In my recent work with clients, I have been thinking a lot about S&OP and how we screwed it up. Let me take you back
On a cold Boston winter day, I slipped into my seat on a back row in a packed conference room at AMR Research. Heavily booked
On Thursday morning, I began an engagement with a food manufacturer attempting to drive “Supply Chain 2.0.” When I asked for a definition, the phone
It has been awhile. After the Supply Chain Insights Global Summit, I took the time to recharge and took a month off from writing. The