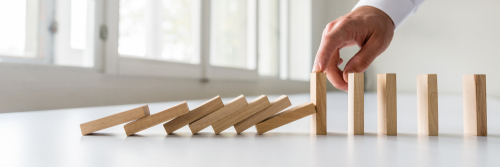
Reflection: The Journey to be Market Driven
In 2002, I had the opportunity to work with General Mills. I walked away thinking, “What a great company!” At that time, the sales organization
In 2002, I had the opportunity to work with General Mills. I walked away thinking, “What a great company!” At that time, the sales organization
Holding my coffee tight, I gingerly slid into the last seat on the bus. It was early morning following a long night of travel. I
The populist narrative of supply chains focuses on sourcing ignoring the impact of historic practices that are no longer best practices creating waste and inefficiencies.
Today’s supply chains focus on cost reduction with the assumption that the reduction in cost will translate to margin. This is not the case.
The lack of organizational degrades value.
Traditional supply chain planning approaches push all products through a common engine to produce time-phased output. The demand stream is analyzed for error and bias, but in traditional processes, companies do not see the patterns. Pattern identification is key to drive successful supply strategies. This is a missed opportunity in traditional approaches.
Like a secretarial typing pool, the definition of work for a supply chain planning is ripe for rethinking work. The redefinition cannot be crawl, walk and run. Instead, companies need to just JUMP!
On Friday, I presented an overview of outside-in planning to a consulting group. I love the questions when I present. The reason? The dialogue helps
The supply chain is a complex, non-linear system. Supply chain excellence is easier to say than define. The Supply Chains to Admire analysis, now in its tenth year and publishes here, celebrates 34 winners.
Supply management. Supply chain management. Supply chain planning. Are these terms the same? They sound similar, but do they describe similar capabilities? The answer is
In a recent blog post, I was challenged by Anna. She wrote, “I have been working in the supply chain for 35 years, and we