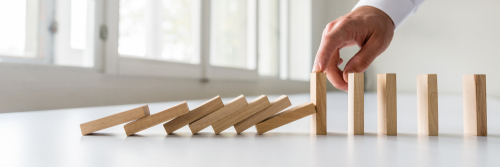
Reflection: The Journey to be Market Driven
In 2002, I had the opportunity to work with General Mills. I walked away thinking, “What a great company!” At that time, the sales organization
In 2002, I had the opportunity to work with General Mills. I walked away thinking, “What a great company!” At that time, the sales organization
Historically, supply chain leaders managed supply chains in a world of abundance. The industry is plunging into a period of scarcity. What does this mean?
Technology can change or even improve work. Companies today making a fundamental mistake: they are attempting to automate current processes with AI versus challenging and
This week, I began teaching a new round of outside-in planning classes. These classes are designed for networking and exploring outside-in models in a safe
Shifting sands. War. Tariffs. Shortages. Price increases. Ocean booking cancellations. Tightening of pocketbooks: changing demand patterns. Decline in consumer confidence. All are unsettling. Companies are
Self-congratulations notes abounded this week as vendor-after-vendor shared their rankings on the Gartner Magic Quadrant for Supply Chain Planning. For me, it was a big
Drip. Drip. Drip. Industry 4.0. DripBig Data. Drip.The Connected Supply Chain. DripDigital Supply Chain. Drip.Autonomous Supply Chain Planning. Drip. Self-Healing Supply Chains. Drip. Touchless Supply
Thirteen years. 600 posts. Where does time go? For over a decade, since founding Supply Chain Insights in 2012, I have pounded the keyboard, asking
This week, I feel like a bobble-head. My head is wobbling with announcements, late-night Friday press releases, company name changes, and executive turnover in the
In December, I spoke at an internal supply chain kick-off for a group of consultants. As I prepped, I noticed a document left on the