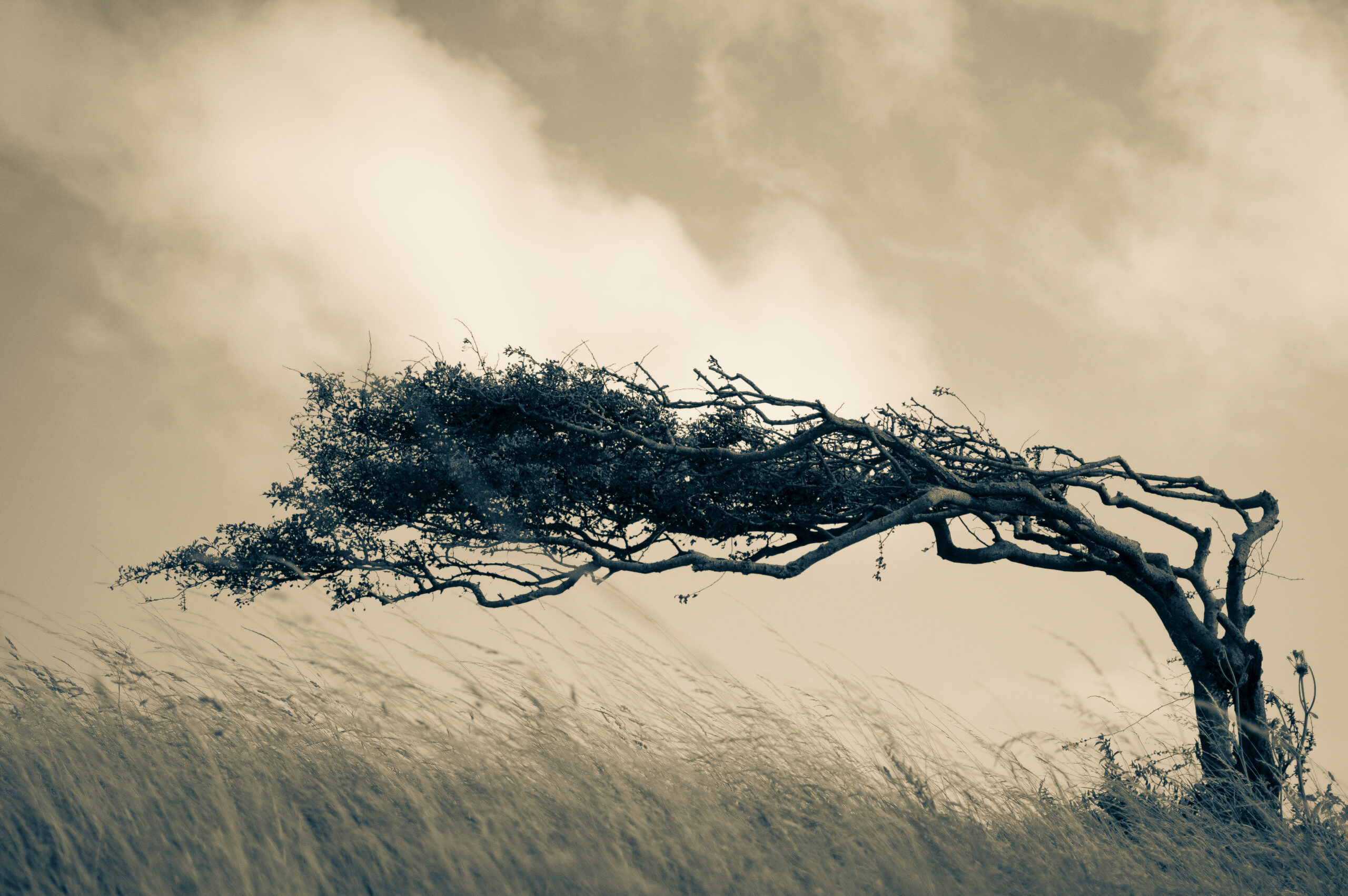
Supply Chain Resilience. Really?
To drive action, supply chain resiliency needs a clear mission and definition. Improving resiliency requires courage to defy convention. Do you have what it takes?
To drive action, supply chain resiliency needs a clear mission and definition. Improving resiliency requires courage to defy convention. Do you have what it takes?
Winds and rising tides threaten homes on Rodanthe Beach. The supply chain software market also has fierce winds and changing tides. In the face of challenges, can E2open survive?
As I flew to Dallas, I worked on this post. Before boarding the plane, I watched a traveler pull a diet Coke from the bin
This morning the Washington Post rang. The reporter wanted to discuss the implications of Hurricane Florence. The question was simple, “What will be the impact
Global growth is slowing to levels of GDP. Notice that the average growth for consumer nondurables (often termed household products) is 1.7%, as shown in
Hyperledger. Blockchain. New concepts? Yes. Get used to it. They are here to stay. I think defining the future of Supply Chain technology means that
It is fall. The hot and humid days are giving way to cool and crisp weather. Today, as I type this blog post, the rain is softly
Today Thoma Bravo, a private equity investment firm, announced a definitive agreement to purchase Elemica, a provider of Supply Chain Operating Networks for the chemical
As an analyst, when technology providers acquire and divest companies, I get invited to pre-announcement conferences. In these sessions the technology providers share their rationale
When I was a small child growing up in the mountains of West Virginia in the United States, on snowy days my family would gather