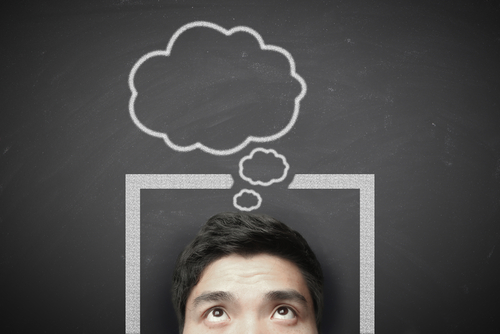
Outside-in Process Q&A
On Friday, I presented an overview of outside-in planning to a consulting group. I love the questions when I present. The reason? The dialogue helps
On Friday, I presented an overview of outside-in planning to a consulting group. I love the questions when I present. The reason? The dialogue helps
In a recent blog post, I was challenged by Anna. She wrote, “I have been working in the supply chain for 35 years, and we
Thoughts on the application of artificial intelligence to supply chain planning.
My Quest To Redefine Planning The focus of many discussion threads on LinkedIn this week focused on building better engines for planning. The discussions included
Sales and Operations Planning (S&OP) is a business process. When the design is a supply chain-centric design, problems arise. I have tracked maturity levels in
Rethinking the role of inventory in inflationary times.
The answer to a simple question of why do consumer products manufacturers not use retail data in the management of the supply chain?
In the face of disruption-after-disruption, now is the time to ask should be redefine supply chain planning and execution. Lora Cecere, Founder of Supply Chain Insights, says it is time. The value proposition is improving the time to make a good decision.
In the past two weeks, I completed many interviews. The question is the same. “When will the impact of the pandemic on the supply chain
Today, we are nearing the end of the fourth quarter of corporate reporting. Self-reported projections of the ocean carriers forecast that the industry is posting