The Saga of Stale Data and Stalled Innovation
This morning, I threw away three loaves of moldy bread....
Turn Off the Fog Machine: Move Past Groupthink to Drive A Positive, Data-Driven Narrative
In this blog post, Lora Cecere, Founder of Supply Chain...
Managing Supply Chain Planning in the World of Scarcity
Historically, supply chain leaders managed supply chains in a world...
Reinventing Supply Chains: Focus on Human Factors
Technology can change or even improve work. Companies today making...
The Bumpy Road to Building Outside-in Processes
This week, I began teaching a new round of outside-in...
The Tale of the Gartner Supply Chain Planning Magic Quadrant and Minestrone Soup
Self-congratulations notes abounded this week as vendor-after-vendor shared their rankings...
How Can You Improve Value in Your Supply Chain?
I laugh when business leaders tell me that they are...
Preparing to Run Supply Chains at the End of the Second Global Economy
Every two weeks, I will be doing a podcast with...
Step Past AI Hype: Drive Real Value
The booths at the National Retail Federation (NRF) on January...
Losing Focus on Serving the Global Multinational
Supply chain leaders readily agree that industry differences exist in...
As The Winds Blow: Improving Supply Chain Planning
The winds of change transform industries. Does a digital transformation...
Passion Drives Supply Chain Planning Forward to Deliver Greater Value
This week, I was introduced by phone to a marketing...
If Only the Supply Chain was Reconfigured
The populist narrative of supply chains focuses on sourcing ignoring...
Build Political Capital to Drive Supply Chain Planning Success
Build political capital to drive a supply chain planning culture.
Redefining Your Relationship with Data
The journey to becoming data-driven requires owning the cycle of...
Navigating the Journey from Cost to Value
Today's supply chains focus on cost reduction with the assumption...
Patterns Tell the Story of Supply Chain Excellence
The use of pattern recognition and orbit charts to study...
Gartner Top 25: The Beauty Contest of Underperformers
Concerned about the impact of the Gartner Top 25 on...
Aligning Supply Chain Metrics to Improve Value
What metrics should supply chain leaders use to drive value?...
Lora Cecere is the Founder and CEO of Supply Chain Insights , the research firm that’s paving new directions in building thought-leading supply chain research. She is also the author of the enterprise software blog Supply Chain Shaman. The blog focuses on the use of enterprise applications to drive supply chain excellence. Her book, Bricks Matter, published in December of 2012.
As an enterprise strategist, Lora focuses on the changing face of enterprise technologies. Her research is designed for the early adopter seeking first mover advantage. Current research topics include the digital consumer, supply chain sensing, demand shaping and revenue management, market-driven value networks, accelerating innovation through open design networks, the evolution of predictive analytics, emerging business intelligence solutions, and technologies to improve safe and secure product delivery.
She comes to the stage with over thirty years of diverse supply chain experience. She spent nine years as an industry analyst with Gartner Group, AMR Research, Altimeter Group and is now the founder of her own firm Supply Chain Insights. Prior to becoming a supply chain analyst she spent fifteen years as a leader in the building of supply chain software at Manugistics and Descartes Systems Group, and twenty years as a supply chain practitioner at Procter & Gamble, Kraft/General Foods, Clorox, and Dreyers Grand Ice Cream (now a division of Nestle).
Subscribe To Our Weekly Newsletter
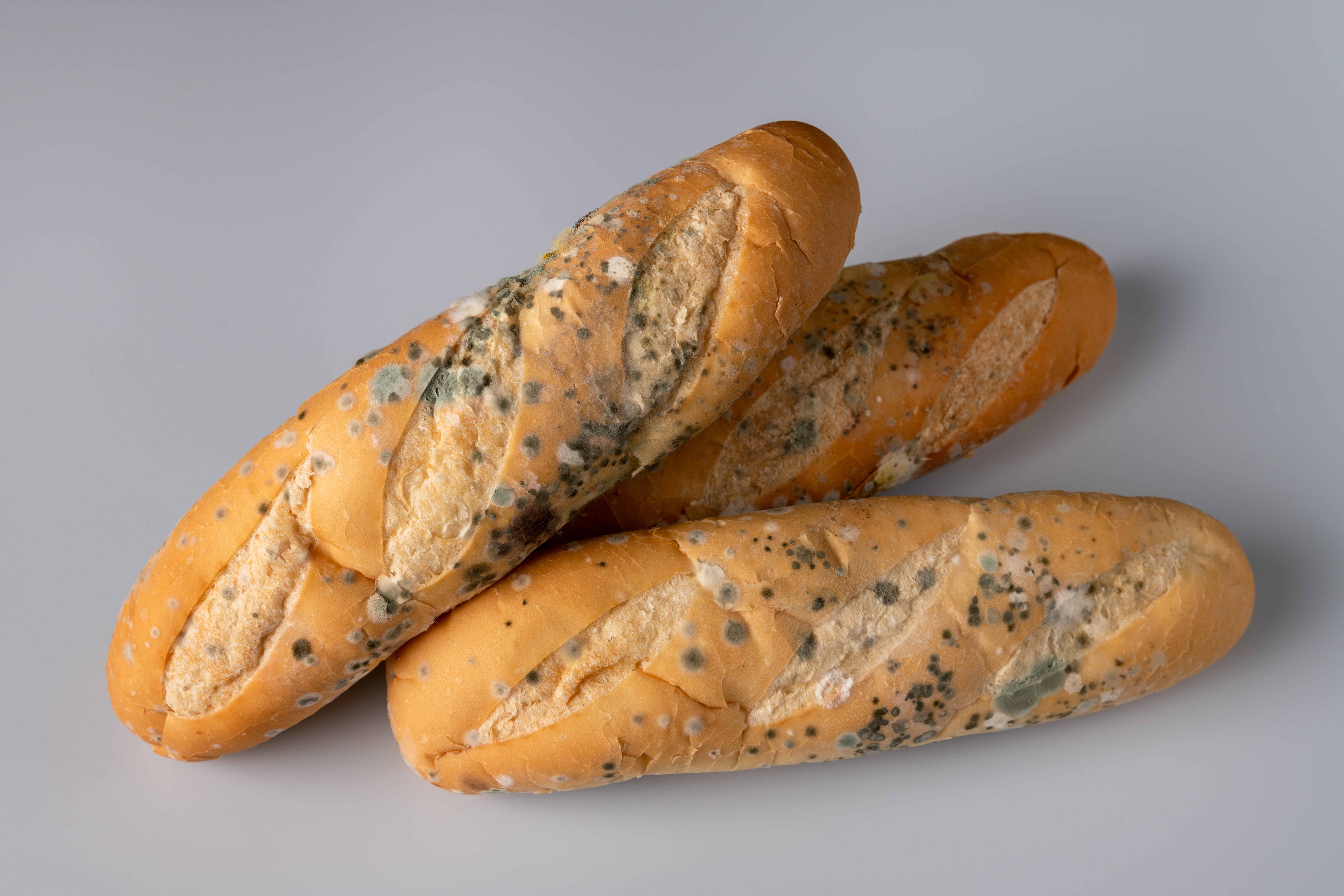
The Saga of Stale Data and Stalled Innovation
This morning, I threw away three loaves of moldy bread. In my attempt to step away from processed food, I don’t buy bread that does
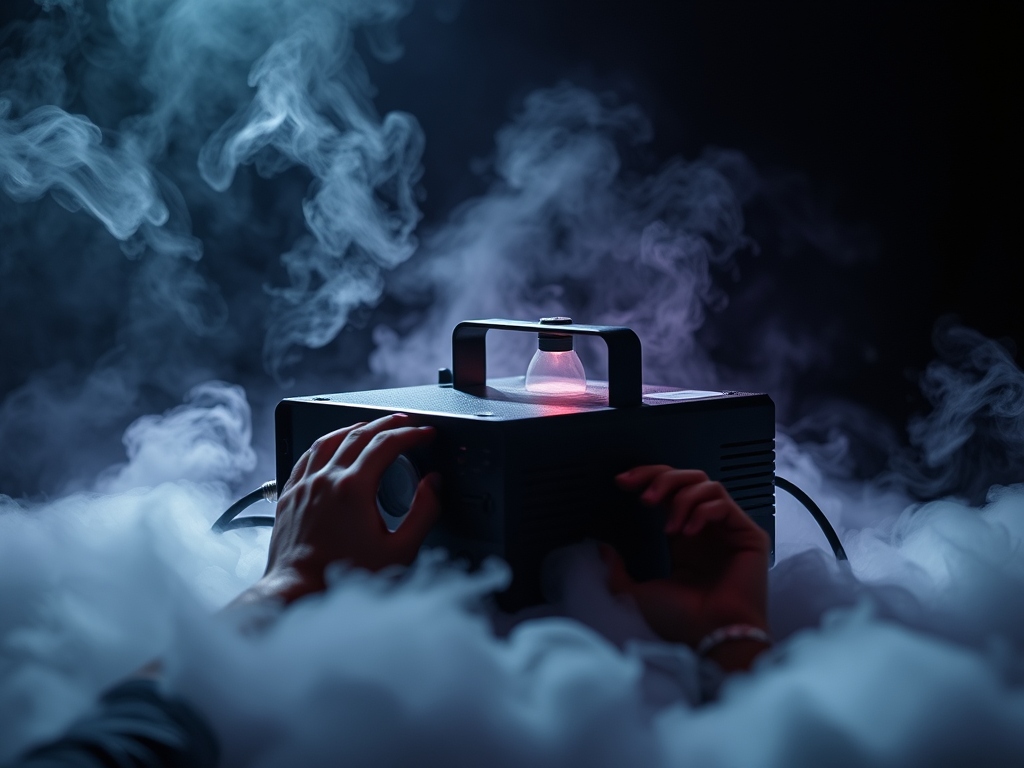
Turn Off the Fog Machine: Move Past Groupthink to Drive A Positive, Data-Driven Narrative
In this blog post, Lora Cecere, Founder of Supply Chain Insights, asks if our current focus on doom and gloom is a fog machine, and a barrier to driving improvement.
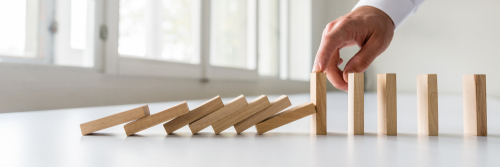
Reflection: The Journey to be Market Driven
In 2002, I had the opportunity to work with General Mills. I walked away thinking, “What a great company!” At that time, the sales organization