I grew up in the mountains of West Virginia. In my youth, my mom would frequently exclaim, “Be careful where you hook your red wagon.” The mountain expression is a warning. My mom wanted me to make smart choices and be careful on placing my bets for the future.
Amazon bought Whole Foods Market. Google is launching autonomous vehicles. There are seismic shifts occurring between industries in value chains. Fear is a powerful motivator. Companies are questioning how to move forward.
Let me give you an example. Last week I spent time with large chemical companies engrossed in this discussion. Sitting four and five levels back in the value chain, and largely stuck on performance, there is a new discussion. The question is, “Did they hook their red wagon to the wrong future?” There are now chartered groups to innovate the business models. In my 15-year tenure as an analyst, I have not encountered such an open audience. So much so, I scratch my head.
Let’s take a look at the world of the chemical manufacturer. In Figure 2, we share the profiles of the companies in the industry. The Supply Chain Index is the rate of supply chain improvement. Usually, a company just starting the journey will make progress faster than a company that has been on the journey for many years. Therefore, a company like BASF with a mature supply chain ranks 25 out of 30 for the post-recession period of 2010-2016.
As shown in Figure 1, the company has been unable to maintain balance on the portfolio of cost and inventory. Acquisitions drove DOW Chemical’s wide swings.
The chemical company’s performance today is largely based on financial engineering (not supply chain excellence). Post-recession growth rates slowed 57% when compared to pre-recession. Cash-to-Cash improved 56.6% largely due to the lengthening of payables. (Note that recent inventory progress is slipping against the improvements during the recession). With a focus on costs, employee productivity improved by 122%; but, this large productivity improvement did not translate into the desired margin in improvement. While the chemical industry improved transactional efficiency through global ERP deployments, the industry has become more reactionary, with a regression in supply chain planning, network design, and strategy. We are now in the transition of passing the baton between generations. Many companies are struggling with shareholder activism. There is a question in the boardroom of “What is possible?” Followed with the question of, “How do we reinvent ourselves?” The commodity chemical, supply-based mindset of bulk shipping, large-scale production, and molecular R&D is shifting to a discussion of new technologies, disintermediation/specialized products, and new business models.
Figure 1. Orbit Chart of Dow Chemical and BASF for the Period of 2006-2016
Figure 2. Performance Data for the Chemical Industry for 2006-2016
I find the discussion stimulating. The confluence of new technologies–additive manufacturing; blockchain; cloud computing; cognitive computing; the Internet of Things; Open Source analytics; robotics; sensors; and wearables– along with process possibilities is driving a new call to action. Fingers crossed, I pray that the debates drive change. Fear is in the eye of the executive team. So, as we talk, I caution:
1) Get Honest. We Don’t Have Best Practices. We Have Historic Processes Built on Technologies from the 1990s. We need to test the status quo. For example, with the Internet of Things, when we sense at the edge, client/server technologies quickly become obsolete. When we plan, and embrace concurrent optimization, planning is redefined through memory and cognitive learning. The convergence of new technologies offers promise, but progress is the fastest with small scrappy teams focused on a goal. Avoid large implementations at this point. Invest in understanding new technologies with a focus on test & learn. After learning, pick where to hitch your red wagon. And then move the red wagon through a governance process to try to drive innovation at the edge, and stability/acceptance at the core.
2) Drive Process Innovation. Take Off the Organizational Handcuffs. Today’s organization is handcuffed by a forced march for IT standardization and process uniformity. Each project requires a defined ROI. It is ludicrous to ask for a ROI on the unknown. As a result, process innovation is difficult. Break the cycle and invest in small projects with an unknown ROI. Build a governance process, like product stage gates, and focus on process innovation. Innovate at the edge and evolve at the core. Evolve both together. (Note: This is very different than the espoused bimodal evolutionary path.)
3) Recognize That the Most Effective Supply Chain Is Not the Most Efficient. Historically, the focus has been on efficient organizational silos. The new opportunity is in value networks and identifying the opportunities between organizational silo initiatives. The focus on horizontal processes, and outside-in sensing, is possible now when it was not a decade ago. The difference? Memory, cloud-based computing and analytics. Investment in ERP is only one piece of the puzzle. It is not the end state. The key is to implement ERP once and well, and then stabilize the transactional system as a system of record. After this accomplishment, invest in new forms of analytics to maximize insights on all forms of data: lakes/streaming data and structured/unstructured data, Think hard about the data that needs to flow through clouds, streams and lakes.
4) Carefully Define the Outcomes. I see a lot of organizations champion cross-functional teams without clarity on goals. When this happens the teams spin. In cross-functional team formation, clarify the goals and make them actionable. As a leader, err on the side of too much information. Give examples, definitions and make it real.
5) Be Open to the Outcome. Have the courage to innovate. This requires organizational learning and change management. Today we don’t have all the answers. The technologies and processes are evolving. Move at the pace of change that is congruent with your DNA. If you are a leader, make strong bets. If you are a laggard, be a smart follower. Clear the road to let the business lead with the help of a smart IT team.
Each time we hook a red wagon, there is an opportunity cost. Be careful. Choose wisely. Avoid long projects and challenge existing business models. Manage hype cycles and evolve. I find this very exciting. If you do also, consider attending the Supply Chain Insights Global Summit on September 5-8, 2017. I hand-pick the speakers and try to facilitate a new discussion to drive new outcomes. We hope to see you there.
This week, I am also sending the congratulations letters to the Supply Chains to Admire winners. For a close-up on the methodology and to gain insights on the 10% of companies making progress, join our webinar on 19 JULY at 1:00 p.m. EDT. Erika Murguia from the Cummins team will be joining me on the webinar to share insights on the culture that has won for multiple consecutive years.
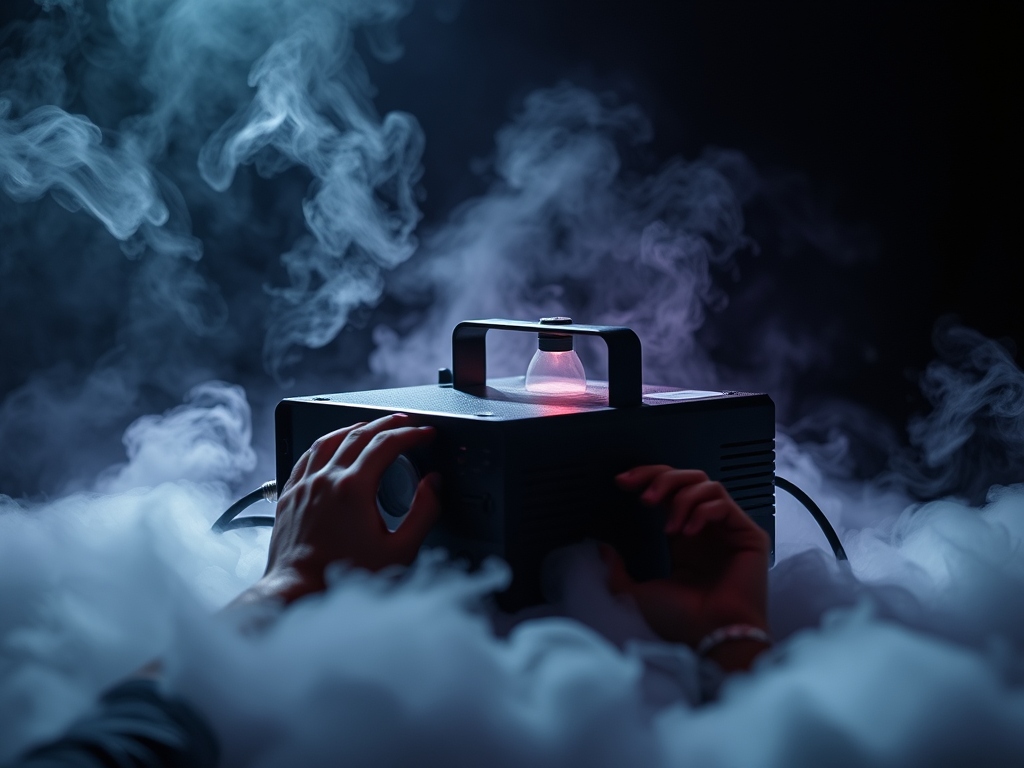
Turn Off the Fog Machine: Move Past Groupthink to Drive A Positive, Data-Driven Narrative
In this blog post, Lora Cecere, Founder of Supply Chain Insights, asks if our current focus on doom and gloom is a fog machine, and a barrier to driving improvement.