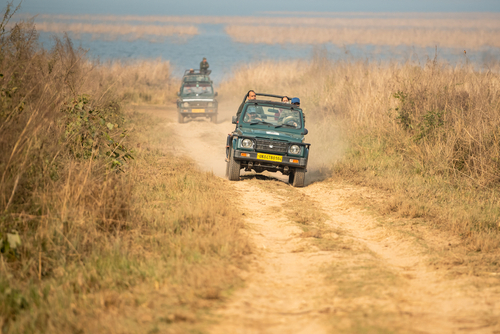
This week, I began teaching a new round of outside-in planning classes. These classes are designed for networking and exploring outside-in models in a safe environment. This is my fourth year of teaching the class and I want to build a guiding coalition for people to think differently and improve value. My goal is to build a guiding coalition for change. I hope that the over 500 students taking the class will start to drive change in their organizations.
As a part of the curriculum, I encourage the class to record their unlearnings because I fundamentally believe that outside-in thinking requires rethinking planning. New forms of technology are an enabler.
I laughed at Neils Van Hove’s recent post. He pushed back on my work in preparation for the class. In my original post, I was trying to share some insights. His view is very different. Here is my reply.
Neil’s post in response to my post of Driving Value From Outside-in Planning:
In her post, ‘Driving Value from Supply Chain Planning’, Lora Cecere provides great supply chain analysis and benchmarking for her supply chains to admire.
The supply chain operating model adjustments and metrics she is suggesting however, are not based on new thinking:
👉 Outside in thinking: in strategy over 50 years old
👉 Outside in demand segmented supply chains: over 20 years old
👉 Business Balanced score card (vertical strategy integration): 40 years old
👉 Aligned strategy execution (strategy management): 20 years old
👉Aligned cross functional incentives: similar to the balanced score card
👉Integrated (horizontal) supply chain planning (S&OP): about 40 years old
👉 Forecast Value Add (FVA): Over a decade old.
We are stuck with old models
Without new thinking, we won’t get unstuck.____________________________
My first response to Niels is “it does not matter how long a process has been around along as it is used and drives value.” The problem is that each of the outside-in processes encountered problems with traditional technologies, and as a result, got stuck and had limited adoption.
Here I want to explore these bumps and share some insights on how new forms of technologies could help us reinvigorate the processes. Before I start, let me share that most of today’s supply chain planning processes are inside-out, rigid and supply-centric. They are artifacts of the schema-on-write world that we have inherited.
Supply chain leaders love shiny objects. They dance in the bright light of these shiny objects at conferences with cell phones in hand depositing smiling selfies all over LinkedIn. I have lived through four hype cycles of outside-in processes. Neils here is some feedback to consider:
- VMI: Vendor-managed inventory logic enables the downstream trading partner to manage inventories and the sell-through the channel. VMI has great promise in the use of channel data and the management of flow. The problem was that VMI is a ship through model whereas supply chain planning is a ship from model with different granularity. The other issue is that VMI only represents a small percentage of the channel. As a result, most VMI processes are managed in sales account teams untethered to supply chain processes. If integrated, they connect at order management, but a missed opportunity is to use the VMI signal as a demand sensing signal into supply chain.
- CPFR: Collaborative Planning, Forecasting and Replenishment garnered great fanfare late in the 1990s. The building of collaborative processes remains an unfulfilled goal. The biggest issue with CPFR was the quality of the customer forecast.
- Flowcasting: The definition is a sell-one/make-one logic using flow from the channel to guide planning logic. The problems are many. First the logic is only appropriate for turn volume items where there is no demand shaping activity. Demand shaping takes several forms–advertising, price incentives, promotions, and new product launch. With demand shaping the logic changes becoming push then pull. With new forms of demand sensing, and the use of different models for different demand streams, the flowcasting logic is appropriate for turn volume models (where items are very forecastable and demand shaping is low), but not the entire demand stream.
- DDMRP: Demand-driven Materials Replenishment Planning is useful for calculating the right buffer for direct materials and improves traditional MRP logic. The problem is that it is order-driven and the order is not a good proxy for demand in make-to-stock and configure-to-order processes.
Neils, the good news is that new approaches of technology can overcome some of these challenges. Should we just put our head in the sand? And, if so, can I come join you down under in Australia? I do love the Gold Coast.
What do others think?