Based on the calls I am doing with the line of business buyer; I believe the buyer of supply chain planning is confused. Not just a little confused, but more so than I have seen in my forty years as an analyst. One of the reasons is technology inflection. The second reason is the discontinued software maintenance support on software from Blue Yonder, Oracle, and SAP. The third issue is the number of failed implementations. The fourth, and an opportunity, is the excitement around the generative Artificial Intelligence (AI) hype cycle.
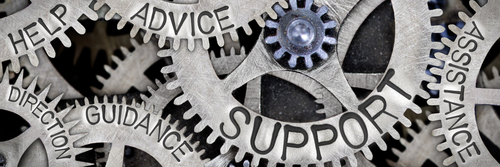
In addition, supply chain planners are retiring. Yesterday, fifteen people in my LinkedIn network left. Each announcement makes me sad. The passing of the generational torch is real.
I am more excited by the Web 2.0 technologies of Graph, NoSQL Unified Data Models, Machine Learning, Unstructured Text Mining/Pattern Recognition, and Narrow AI than Generative AI, but I find a low level of understanding by the average buyer on the promise of these platform elements. The buyer is very confused and struggles to speak the language of supply chain planning. Most RFPs in the market are trainwrecks. The discussions are in the weeds, and few see the need to see the sky. Many are the wrong discussions. So what should you do? In my upcoming strategy days, I recommend seven steps:
- Step 1. Shift From Inputs and Outputs to Drive Outcomes. Most technology discussions are focused on feature-function diatribes versus driving business outcomes. Now is a great time to shift your programs to improve value. Redefine work. Why don’t we build self-learning supply chains to enable business leaders self-service to gain their insights and drive peer collaboration? We have self-service HR systems. Why not self-service demand and supply planning? Organizations have grown the number of planners exponentially without driving improved value. Redefine the planner’s role to be an orchestrator and move decision support to be a self-service application by business leaders.
- Step 2. Measure and Drive Learning Systems. Measure. Learn. Adapt. Just don’t say Net Zero measure the impact. Don’t talk about the bullwhip effect. Instead, measure and harness it. Redefine demand management by measuring Forecast Value Added (FVA), demand latency, bias, and error. Improve manufacturing by measuring schedule adherence and first-pass yield. Build a scorecard for executives to enable visibility of plan effectiveness and recommendations for future improvement. Drive learning systems to improve value through measurement.
- Step 3. Design Using a Balanced Scorecard. Only 9% of supply chains are designed, and network design technologies focus primarily on asset utilization. Shift the use of design technologies and what-if analysis platforms to manage supply chain flows. Each supply chain has four to five flows. Each needs to be managed. Provide visualization and learning systems to improve decision support.
- Step 4. Shift from Feature/Function Focus to Value. Most company demonstrations start and end with feature function. (These discussions are so boring. I want to engage technologists on how technology can improve work. Move past feature function in today’s processes to unleash new value. Don’t paint in the box of existing technology taxonomies. Instead, observe and push for technology to harness new value through learning systems.
- Step 5. Shift from Transactional Views to Flow. Harness and Visualize Flow. Transactional paradigms are shifting to flow. While order-to-cash and procure-to-pay are clearly transactional solutions, decision-support processes are moving to flow. Visualize and manage demand and supply flows and improve reliability.
- Step 6. Create Safe Zone Areas for Business Leaders and Technologists to Think Deeply and Solve Problems. Build open networks to enable innovation between technologists and business leaders. Ask innovators to send you their biggest hairiest problems through open design networks. Side-step the RFP process.
- Step 7. Use Generative AI for Content Development. Shipping instructions. User guides. Training materials. These are all good use cases for generative AI. I don’t think we are ready to use generative AI as an engine in supply chain planning. The reason? The organization is not aligned on the definition of supply chain excellence. Alignment issues grew three-fold over the last decade with a rise in politics in large organizations.
The goal is to build methodologies to drive success. Recently, I audited a large technology company’s multiple implementations. The results were dismal. Analyze the quality of data before starting, and test engines. Ensure plan feasibility and train the team. Analyze the effectiveness of the software post implementation by remote views of the balanced scorecard and learning systems.
Test to ensure that the planning process is driving better outcomes. Put the data on the desk of the Chief Supply Chain Officer, the Chief Operating Officer and the Chief Financial Officer’s desk and help drive awareness and organizational alignment.
I hope this helps. What am I missing? What would you do?